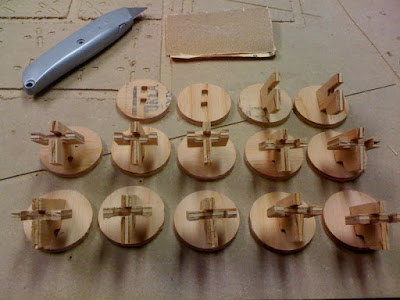
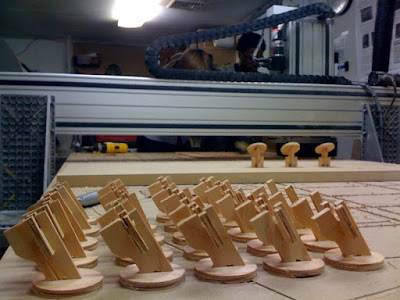
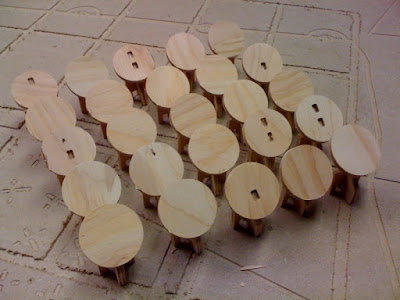
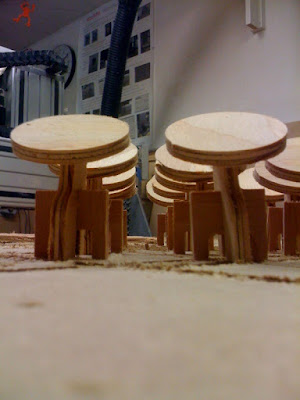
manually set the z axis 1/2" high during the pocket hole run in order to prevent cutting through as happened with the test pixels, then reset at 0 for profile cuts
adaptation worked, for the most part, except where bowing of the plywood caused the material to sit too high at some cuts.
other learning from failures...
*we did not take into account the difference in orientation of cut for the pockets and tabs. pockets have rounded edges, tabs have square edges. so...square peg, round hole. this required a touch of sanding and/or forcing in assembly.
* plywood is bad for small/intricate pieces (especially the cheap stuff). it tends to separate at the laminations, counter to the actual depth of a pass, making breaks and jagged cuts.
* extra pieces = good
* we had issues with the material bowing and raising on the profile cuts as well. because we didn't place drill holes in the mastercam file, interior support screws were done ad hoc, during the milling process. not ideal.
No comments:
Post a Comment